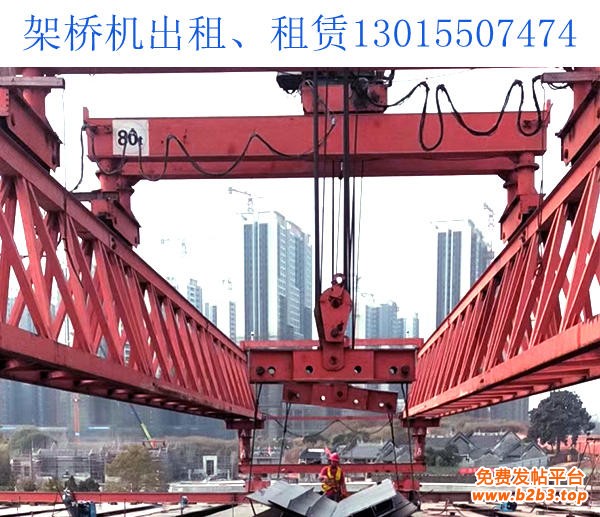
一、前期准备阶段:压缩 “等待时间”,减少无效作业
前期准备是效率提升的 “隐形突破口”,需通过标准化、工具化、数字化缩短检查与匹配耗时。
(1)数字化检查清单替代人工核验:传统人工逐项检查(如吊具磨损、传感器状态)需 30-40 分钟,可升级为 “智能检查系统”:通过安装在吊具、卷扬机、滑轮组上的传感器(振动传感器、磨损传感器),实时采集数据(如钢丝绳断丝数量、销轴间隙),系统自动生成 “合格 / 不合格” 报告,仅需 5-10 分钟完成全项检查。
(2)吊具 “快速连接 + 通用化” 改造
针对不同梁型的吊点差异,设计 “模块化吊具”:通过可调节吊耳间距、快速锁止销轴,实现 “一吊具适配多梁型”,避免频繁更换吊具。
配套 “吊点预定位装置”:在预制梁场或运梁车上预设激光定位点,吊具下降时通过激光传感器自动对齐吊点,减少人工肉眼调整时间。
二、核心作业阶段:提升 “有效作业速度”,减少调整次数
起吊、移位、落梁是起重系统的核心耗时环节,需通过技术升级提升动作流畅性,减少 “反复调整” 导致的时间浪费。
(1)起升阶段:优化速度曲线,减少 “试吊 - 调整” 循环
传统试吊需 “起升 - 停止 - 检查 - 再起升”,可通过 “智能试吊系统” 优化:利用称重传感器实时采集梁体离地瞬间的受力分布,系统自动判断 “各吊点受力是否均衡”,无需人工肉眼检查,试吊时间从 5 分钟压缩至 1 分钟。采用变频调速技术:将起升速度分为 “低速试吊- 中速提升- 高速运行” 三档,根据梁体高度自动切换,32 米箱梁的起升时间可从 15 分钟缩短至 8 分钟。
(2)移位阶段:升级 “防摇 + 对位” 技术,减少姿态调整
传统移位时,梁体因惯性或风载会产生 ±30cm 晃动,需反复调整小车位置。可通过以下技术解决:
安装主动防摇系统:基于陀螺仪和位移传感器实时监测梁体晃动角度,系统自动控制起重小车反向微动,抵消惯性力,将晃动幅度控制在 ±5cm 内,移位过程无需停顿调整。
引入自动化对位系统:在桥墩和梁体上安装 GPS 或 UWB 定位标签,通过控制系统自动计算起重小车的横向 / 纵向位移量,驱动小车精准移动至待架位置(对位时间从 20 分钟缩短至 5 分钟)。
(3)落梁阶段:精准控制 “下降 - 校准” 节奏,减少重复调整
落梁的核心耗时在于 “高度校准” 和 “水平度调整”,可通过以下优化:
升级高程监测系统:在吊具上安装激光测距仪(测量精度 ±1mm),实时反馈梁体底部与支座的距离,结合卷扬机编码器精确控制下降量,无需人工反复测量。
采用同步调平油缸:传统调平需分别操作两侧油缸,改为电液同步控制系统,通过位移传感器实时对比两侧油缸行程(偏差<1mm),一键完成水平度调整。
三、设备性能:提升 “可靠性”,减少故障停机
起重系统的效率受限于设备稳定性 —— 频繁故障(如钢丝绳断丝、卷扬机卡滞)会导致 “非计划停机”,需通过硬件升级和维护优化降低故障率。
(1)关键部件升级
钢丝绳:选用压实股钢丝绳,配合钢丝绳自动润滑系统,减少因磨损导致的更换频率。
卷扬机:采用行星齿轮减速器,搭配大功率电机,在保证扭矩的同时提升运行速度,且发热减少 50%,避免因过热停机。
制动系统:升级为液压盘式制动器,配合双重制动(电磁制动 + 机械抱闸),减少因制动故障导致的 “溜钩” 风险,无需频繁停机检查。
(2)预防性维护机制
建立数字化维护清单:通过传感器实时采集卷扬机电流、制动片磨损量、吊具销轴间隙等数据,系统自动预警 “即将超限项”,避免故障突发。
制定 “作业 - 维护” 联动计划:例如每架设 50 榀梁后,利用夜间窗口期进行 “快速保养”(更换润滑油、检查销轴),避免白天作业时占用有效时间。
四、管理与协同:优化 “人机配合”,减少流程内耗
效率提升不仅依赖技术,更需通过标准化流程和人员协同减少 “人为失误” 和 “衔接断层”。
(1)作业流程标准化
制定《起重系统效率手册》:明确各环节的 “时间基准”,并标注 “关键节点”(如吊具连接必须用扭矩扳手,避免因松动返工)。
引入 “节拍化作业”:将架梁全过程分解为 “取梁 - 起吊 - 移位 - 落梁 - 吊具复位” 5 个步骤,每个步骤明确 “操作人、工具、耗时”,如 “起重司机负责起升,地面指挥负责对位,两人通过对讲机实时确认,避免重复沟通”。
(2)人员技能提升
开展 “模拟 + 实操” 培训:利用 VR 模拟器训练司机应对 “突发晃动”“传感器报警” 等场景,提升应急处理速度。
建立 “效率激励机制”:对单榀梁架设时间低于基准值的团队给予奖励,激发主动优化意识。
五、安全与效率的平衡:避免 “因快失稳”
需强调:效率提升必须以安全为前提,禁止为提速牺牲核心安全环节 —— 例如超载限制器、高度限位器不得擅自调整参数;风速超过 6 级时必须停止作业(避免强风导致梁体失控);试吊环节(离地 10cm 检查)不可省略(防止吊具连接失效)。
2.架桥机起重系统的效率提升是 “技术升级(占 60%)+ 流程优化(20%)+ 管理协同(20%)”的综合结果。实际应用中,需结合项目特点(如梁型、工期、环境)选择适配方案 —例如高铁项目对精度要求高,优先升级自动化对位和防摇系统;公路项目对速度敏感,可侧重变频调速和吊具快速连接。通过系统性优化,单榀梁的起重作业时间可从传统的 40-50 分钟压缩至 20-25 分钟,显著提升架桥进度。
3.山西朔州架桥机销售公司13015507474坚守对细节的极致追求,以客户的需求和期待为核心导向,打造出辐射广泛的服务网络。一心致力于为客户带来专业规范、形式多样的服务体验,依托出众的产品表现、更优的成本效益与富有人情味的服务宗旨,不断为客户创造真实价值 。
电话:13015507474
网址:http://www.gdthqzj.com/